A complete and entirely unintentional over-correction
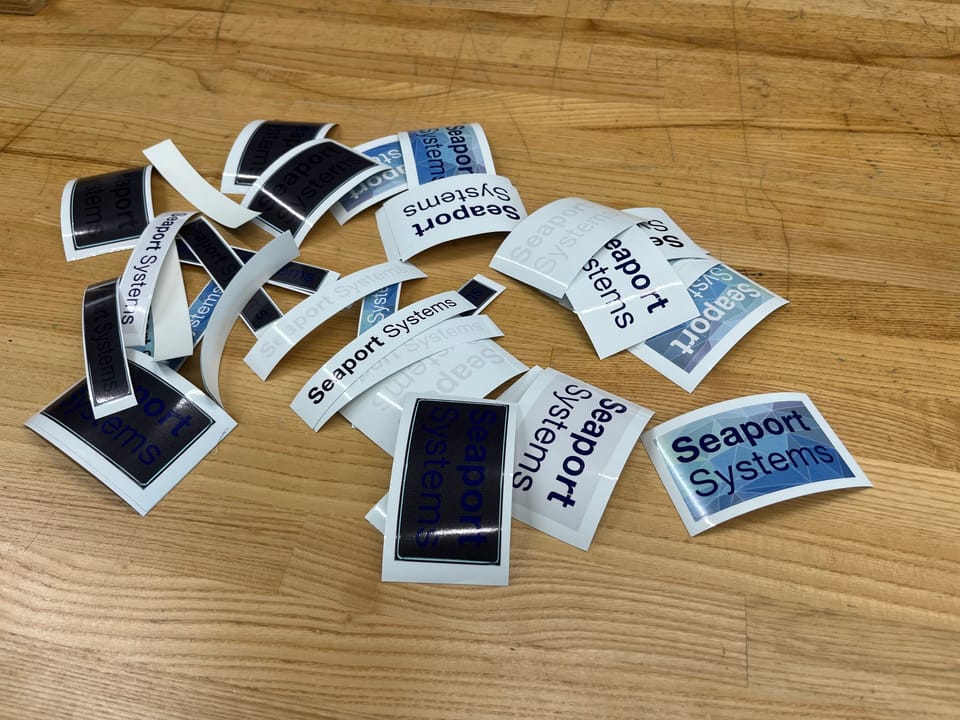
Ahoy!
This Week
Unlike last week, when I was laser focused, this week has been all over the place. Side-questing galore! Basically, the consulting project I was working on last year is still going on, but I've been in more of an on-call situation. Get to work early waiting for an update from the night crew, do any work that needs doing, then wait for something to break or otherwise come up. All in all, the project is only taking ~2 hours of my time everyday, but it's usually 15-30 minutes at a time every hour or two. Ultimately, it's been really hard to commit time to any other project - it takes 15 minutes to shift focus from whatever I'm doing to this project, do the work, write it up, then shift focus back to whatever I was doing initially. So, as embarrassed as I am, I didn't move the needle on anything particularly impactful. I still managed to make something of that time, rather than just scrolling!

As it turns out, the haphazard schedule is perfect for tasks in the Not Urgent half of the Eisenhower Matrix.
The Eisenhower Matrix is a way of categorizing a task into one of four quadrants based on its importance and urgency. I'm not great about using it yet, but knowing about it has given me a new tool and framework for thinking about work.
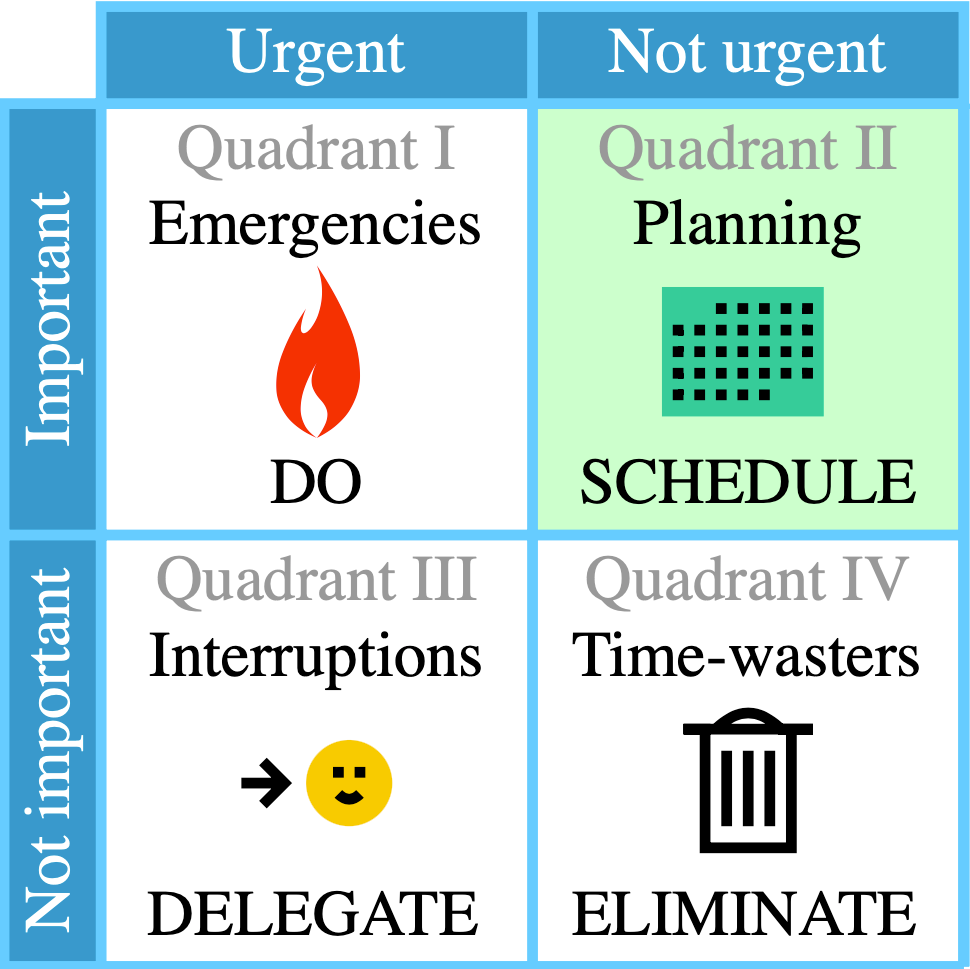
Branding
Branding, graphic design, etc. is a great example of an Important + Not Urgent task. Without getting too philosophical, branding/image is really important to me, and it's something I want to do incredibly intentionally. That's part of the reason the rebranding to Seaport Systems took well over a year - I wanted to make sure I got it right the first time (well, the second time technically, but whatever).
At the turn of the year, I built out a very basic branding guidelines document. It lays out things like brand colors, fonts, styles, etc. It certainly isn't exhaustive, but realistically it was a great start. The guidelines are great for laying out how to design things consistently, but isn't actually a useful deployment of design. So this week, I put it to work!
The first thing I did was spend time in Affinity Designer building out every possible logo combination - logo colors, background colors, form factor. In the past when it came to branding things, it was because I was in a rush, but this week I took time to actually learn how to use the program and format my work in a stable, usable way.
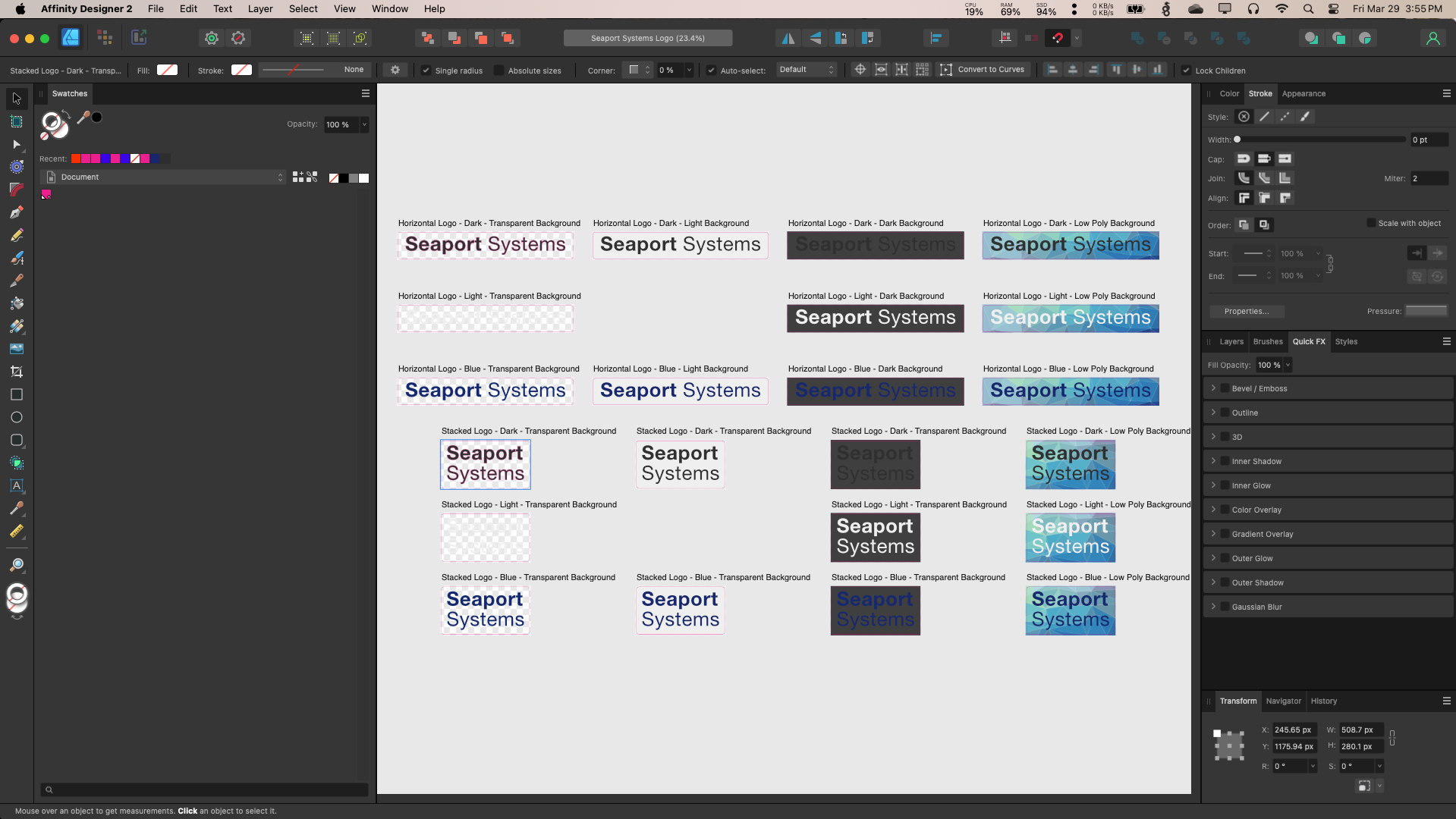
Stickers
Next, I took all those logos and ran them off as stickers! I exported every logo variation I had, and printed them on vinyl before having them cut out. I'm a firm believer in committing work to the appropriate physical medium. Instead of being an infinitely adjustable idea on the computer, a physical representation is a commitment, which I think a lot of people get hung up on - If they're going to make something it better be perfect. Perfect is the enemy of good. I know a few people who are incredibly good at countering this. They'll come to me a couple times a day and ask for me to critique something they made. Not once have they pulled me over to their computer and asked me to look at something in Word or PowerPoint or CAD. Even if it's just a document, I get a print. That's critical. It's too hard to review or revise something that's completely dynamic. It's far more productive to pick something up, say "here's everything right and wrong with this". You'll never get it right the first time, you might as well commit to a few iterations, you'll need them in the end no matter what
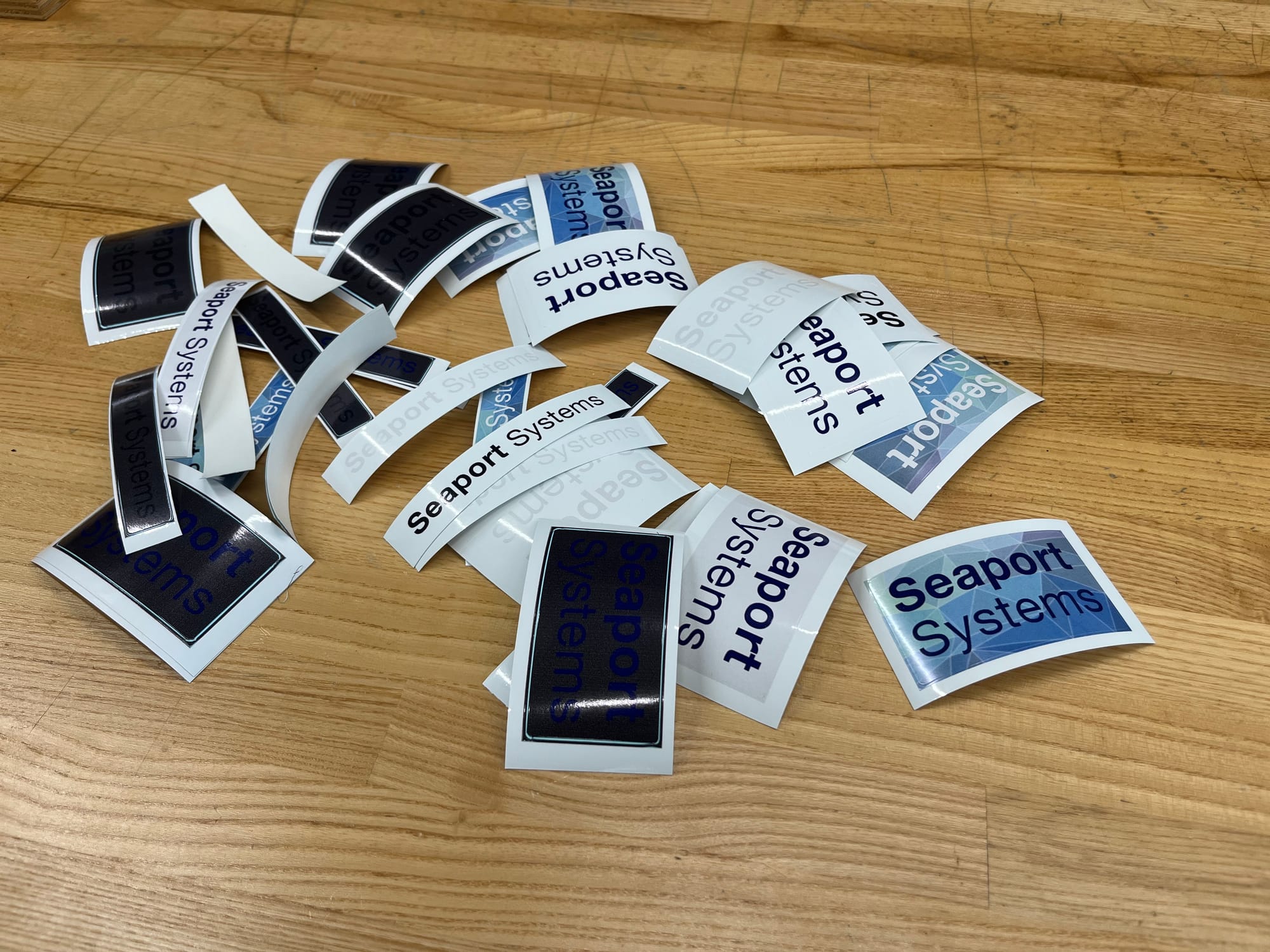
T-Shirts
I've always wanted company merch. I think it's a cool way to share my adventure with friends, family and customers. A branded t-shirt can go a long way for first impressions at a trade show or visiting with a potential customer you don't have a rapport with. I always assumed it was pretty complicated and expensive. I don't have $100 for an embroidered polo shirt, and I don't have $1,000 for three hundred something t-shirts. Furthermore, I have no need for hundreds of t-shirts, and my girlfriend would kill me if I tried to keep them in our apartment. In my sticker quest however, I've discovered heat transfer vinyl. You cut out the vinyl like normal, peel back a layer, apply it to just about any garment, apply heat, and voila! I'm stoked. I was joking with some old friends - if I had known making custom shirts was this easy, I would've been in wayyyyyy more trouble in high school!
In the immediate term, I'm just trying to make a few for myself that I can wear when meeting customers or other important people. I've tested a couple different shirts and logos. My goal is for a super-minimal, very clean design and I'm liking the first couple of iterations so far! I've got some ideas from different folks I'll try out, but my hope is that this project is completed this weekend.
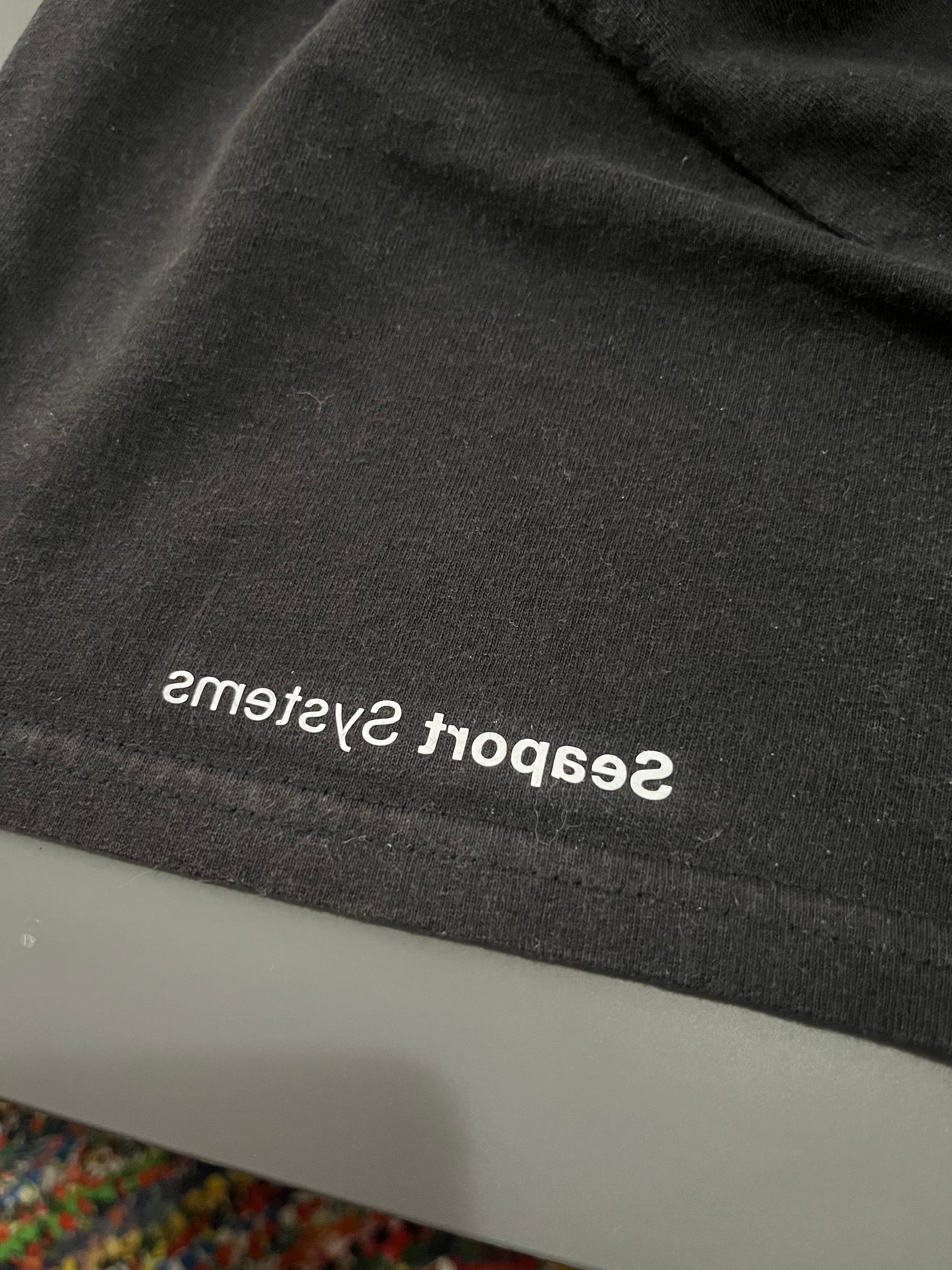
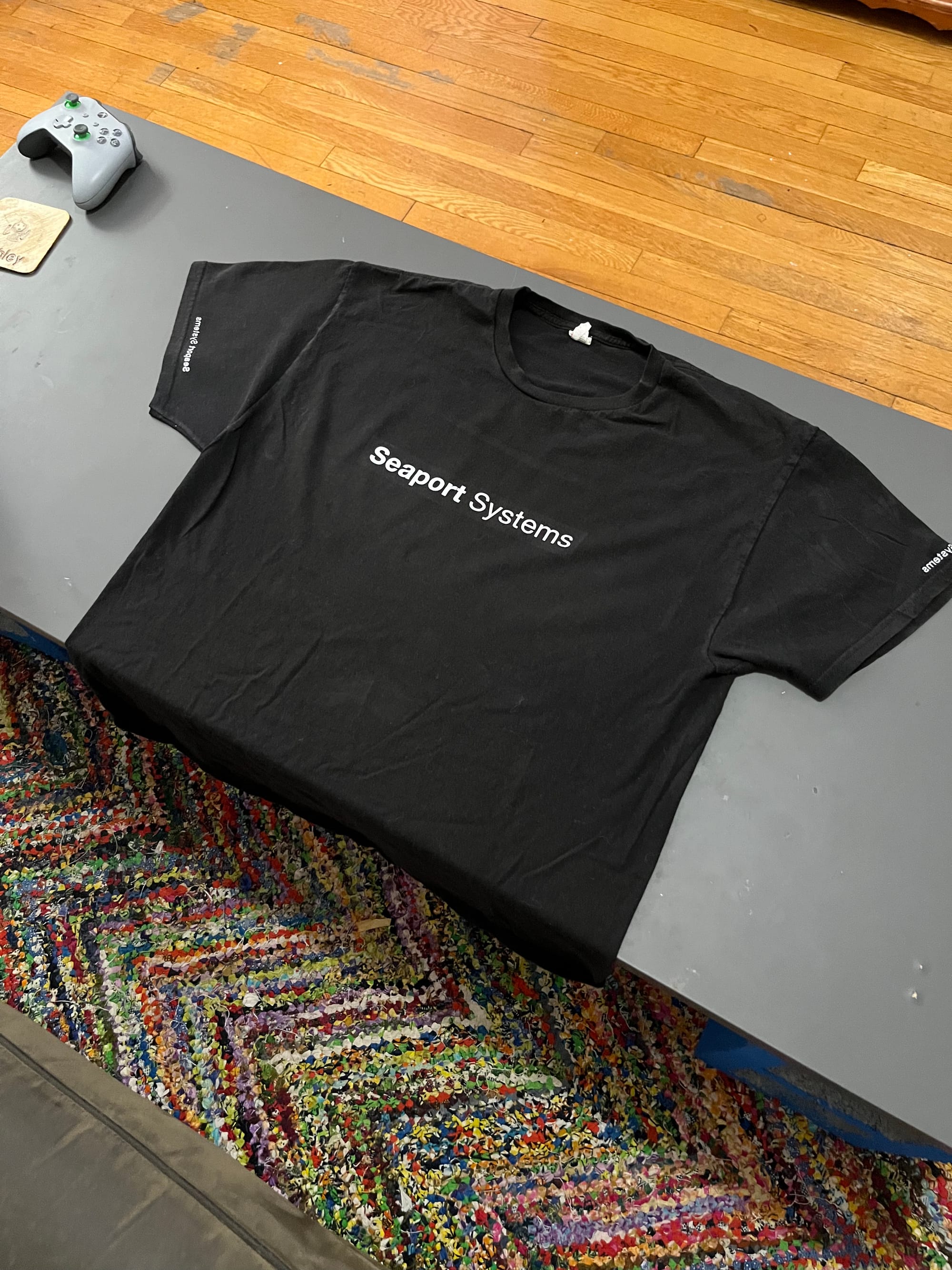
Didn't realize I had to flip the graphics initially... It's also incredibly hard to take a downward photo without also taking a picture of your feet, and this is not that kind of blog...
Title Block
I've gone on enough about frivolous branding things, but a slightly more productive outlet for this has been in Seaport System's Title Block/Drawing Template. Basically, any part or assembly that gets made, and anything that gets made has a technical drawing. I spent a good amount of time dialing in the template for all future technical drawings, which I will need very soon. Like the rest of the branding, I want it to be minimal, visually appealing, and also still good at presenting the information it's meant to. Much harder than I imagined...
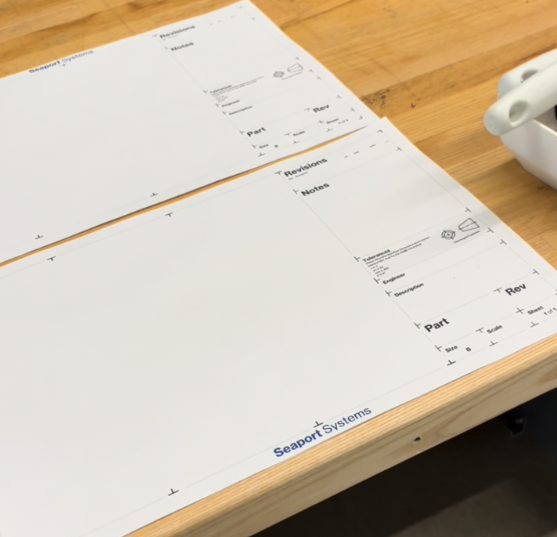
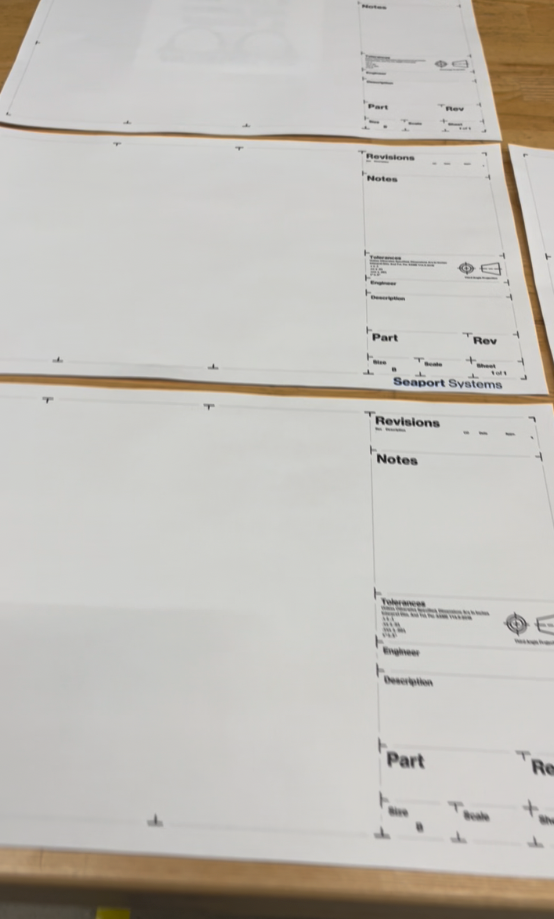
Many many iterations
Prep Work
Progression on the XB-X/MB-X Top Collar was a big goal of mine from last week. I haven't cut chips on the full scale part yet, but it's near. The biggest issue with making this part has been how to hold it while milling it. With some help and advice from the machinist at work, I think we're going to try holding it with soft jaws and VersaGrips. The VersaGrips are great because, unlike other teeth/clamps/jaws, the versa grips are able to rotate in place which means they're great at conforming to weirdly shaped parts. So we've got a good potential solution, and I've received the material the Top Collars will be made from. The biggest unknowns/blockers have been resolved and we should have a fruitful week.
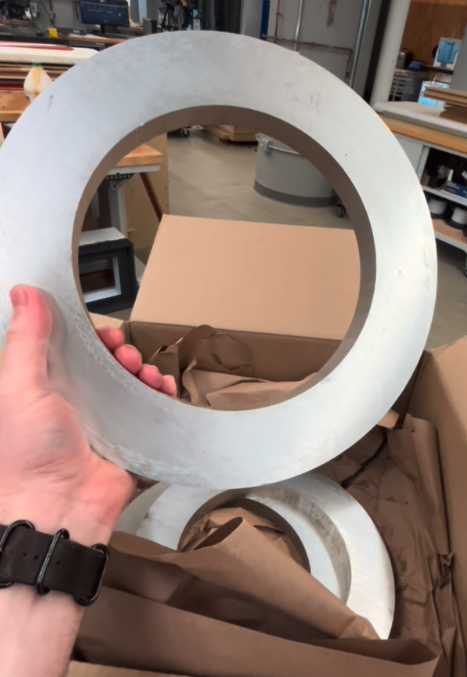
I have not made any progress on the DB-X stabilizers this week, but I'll issue a slight correction to my description of their function. Drifters like the DB-X are designed to get tossed out into the water, then drift with the currents. Ideally, a drifter will move at the same velocity as the water. It's easy to take this property for granted, but it's actually quite challenging. The buoy can't be too light, otherwise the wind might blow it around. It can't be too heavy, otherwise the water current won't be able to get it up to speed. So the stabilizers are designed to optimize the relationship between the water and the buoy, so the velocities can match as closely as possible.
Antennas for the DB-X have arrived and I've done some initial modifications and fitment. They're looking promising, but deserve an exhaustive test campaign. I think I might come in to work tomorrow to work on some of that!
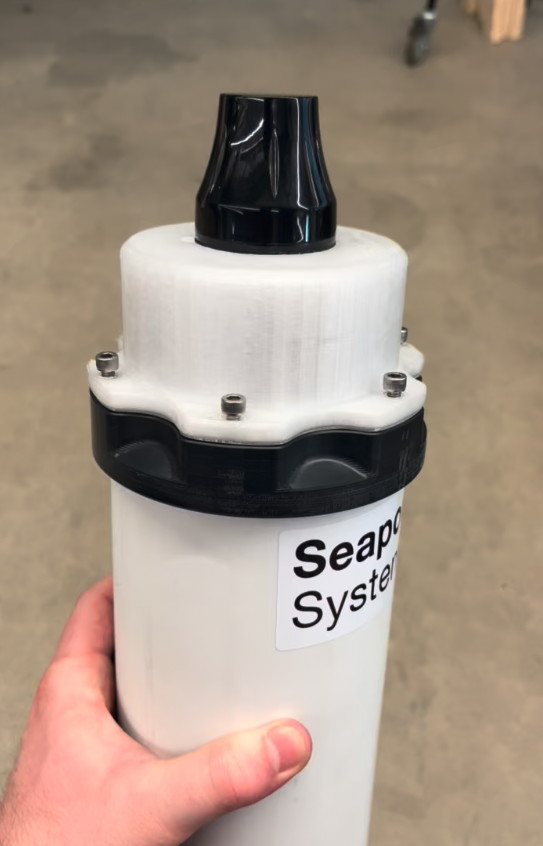
Next Week
Top Collar Machining
See Prep Work above...
Antenna Testing
Again, see Prep Work above...
Stabilizer Design
I'm starting to see a pattern I'm not sure I like...
Wins
Merch
A few super cool t-shirts I can wear, and a ton of stickers I can plaster all over the place.
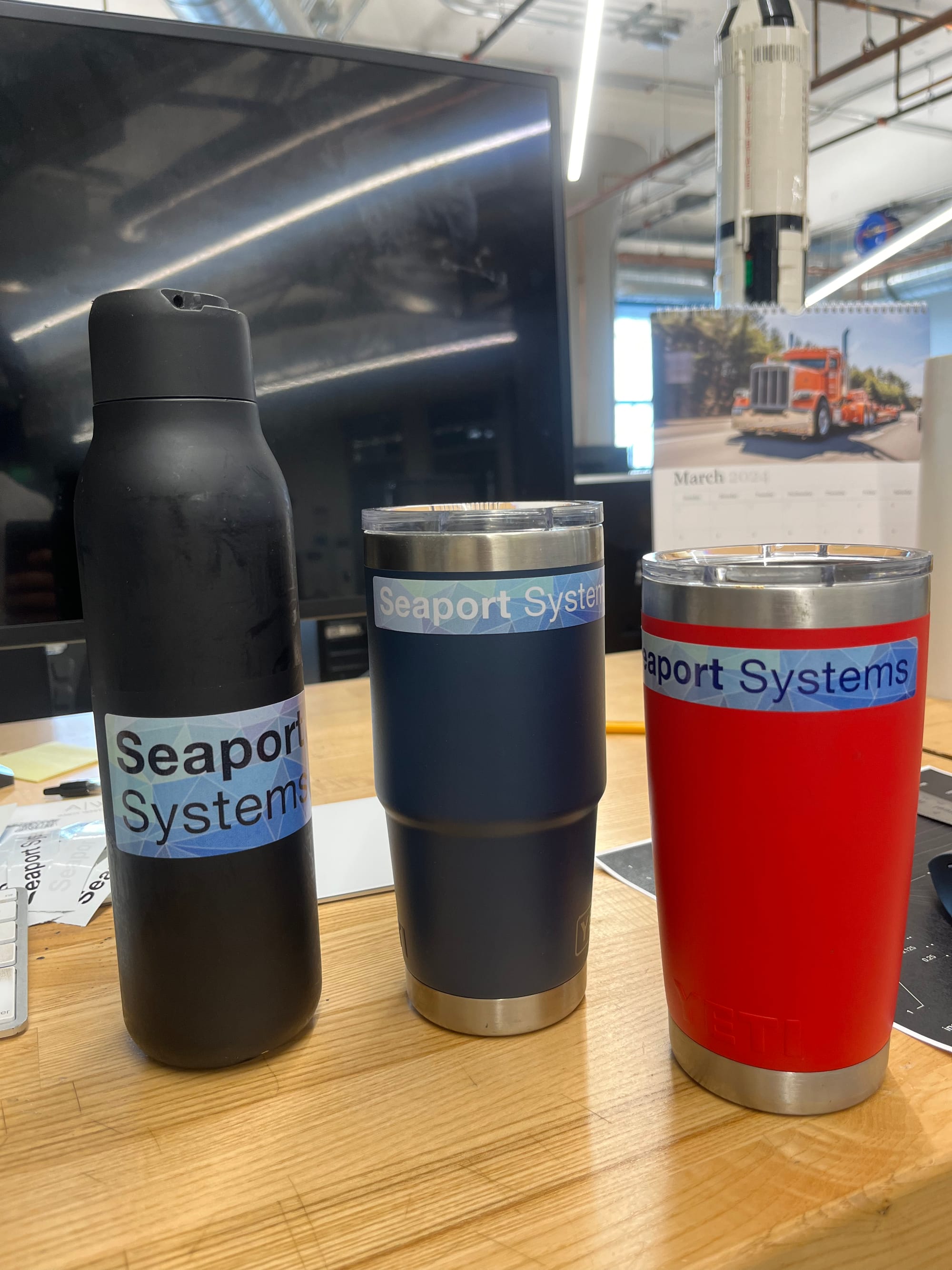
Carlos Sainz
He won, not me, but I'm happy for him despite being a Checo fan. Maybe I should have my appendix removed too.
Losses
I didn't complete a single thing I set out to do last week. I made some progress, but ultimately I fell short. All I can do at this point is correct the problem in the future.
Train Track of the Day
Kinda forgot about the blog until lunch - rushing to get this out before people either hit their commute home or start partying. Maybe I'll write it on Thursday night next week... That way I can reflect on the writing, take time to edit it, then send it out. Planning, who'd have thought!