Thoughts on Tools For Making Things
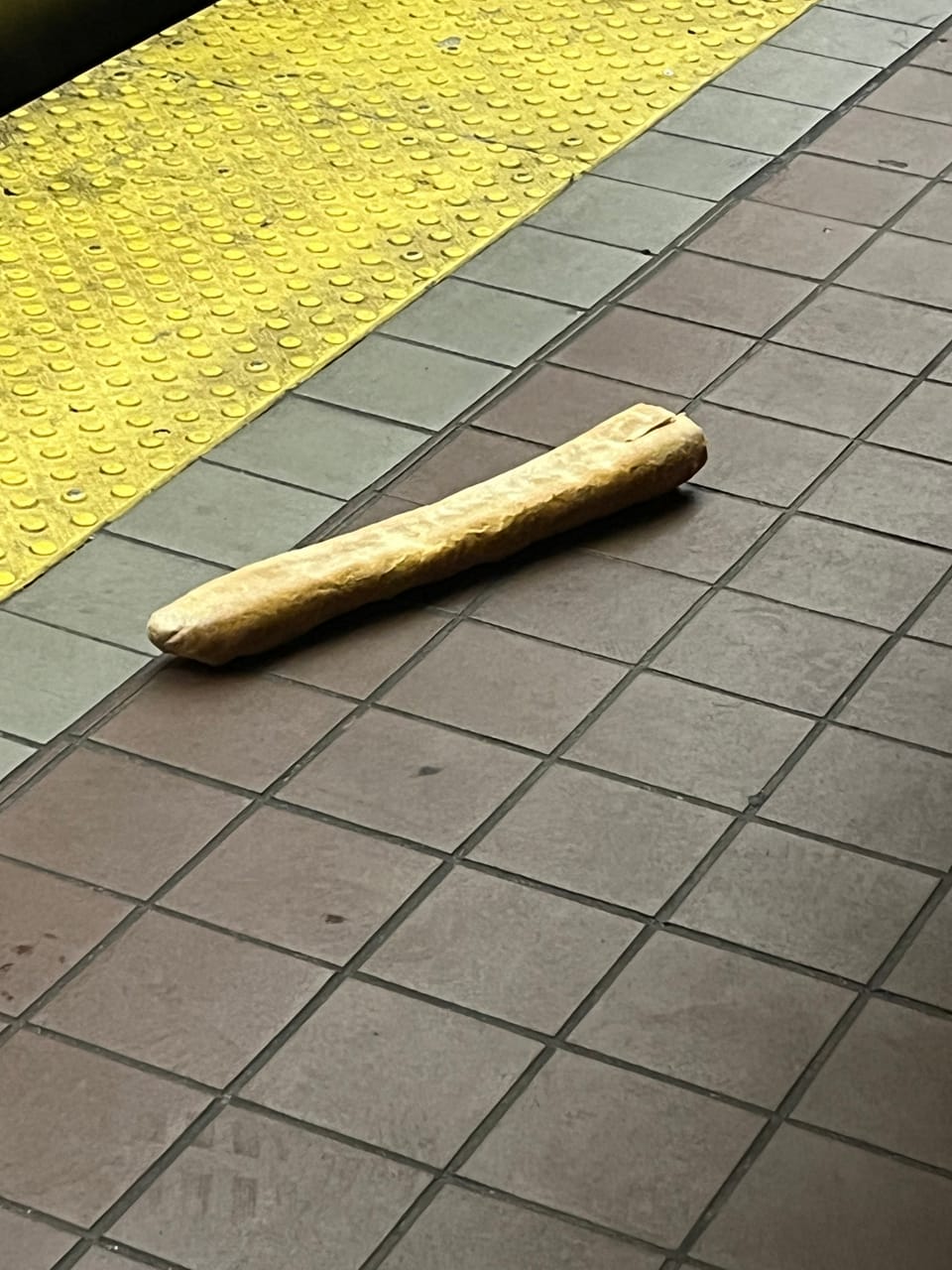
Welcome back! You can catch my most recent ramblings in the top half of the blog, and project updates in the back 9.
Several Thoughts On Tools That Help Make Things
To anyone who writes professionally, or even just regularly: how do you begin? When I start, I sit down and start typing random gibberish. I rarely go into it with a train of thought or thesis. I just type until something coherent appears, or I happen upon an idea worth exploring. It feels like what I'd imagine making pottery is like. I'd say this process kind of works, but I think in the end I end up rambling. It's too easy to skip from thought to thought. Some ideas end up under explored, others overstated; and the connections between them are thin.
There it is! The rambling has led me to something I want to write about: processes, frameworks and tools. Cool.
Different industries, professions, jobs, hobbies, etc. have many different ways of doing the same thing. Brainstorming and idea creation for example, as I started above. A writer starting a novel, a pottery person (potter? potterist? thrower? pitcher?) beginning a bowl, an engineer building a buoy all start without any idea of what the final form will look like. (Maybe they do have an initial idea, but humor me for a second, or however long it takes you to read this). I'm not really a writer, so I don't actually know how they'd begin. A potter may grab a chunk of clay, put it on the wheel and start shaping at random until something feels right. An artist or musician may travel or immerse themselves in a culture, or activity waiting to be inspired. An engineer or woodworker would probably sit down with requirements/functions and start sketching solutions. We're all trying to do the same thing, but we all have drastically different, sometimes specialized, processes.
In hindsight, it's fairly easy to see evolution - be it a tool, a process or idea. It's usually much harder to commit to a change or evolution intentionally. I'd say it's rare for an engineer to sit down and design a part like a writer would build a world, and vice-versa. But there's so much opportunity for innovation and creation when we cross-over like this.
While incredibly niche, and I may lose some of you, I'm going to use a more real life example of this. When you set out to build something, you're almost always doing so collaboratively. There is a process and framework for people to combine their work, some more elegant than others. The example most people will think of is Google Docs or Office 365. In software engineering there's a similar, incredibly slick category of tools called version control. Git is a popular example, that allows programmers to work on the same codebase (10s, 100s, 1000s of files that all intertwine to rule the world, I, erm, mean become usable software). Git provides really neat and unprecedented features that allow multiple programmers to change the same file, and reconcile all those changes in a way that is desirable to everyone. I don't need to get into the mechanics of it, but I think everyone could use a flavor of Git.
The functionality that Git provides software developers to collaborate is something that I haven't really seen adopted in the rest of engineering. The most synonymous example of this is CAD. Today, engineers design physical objects and assemble them in Computer Aided Design (CAD) files, fancy word for 3D models. Decades ago, an engineer made a physical drawing of a part. If another person wanted to make a change, they'd have to go to the original engineer or the filing cabinet that had the drawing, take it, make the changes themselves, then hopefully return it. Even the most sophisticated software for managing these files today, is essentially just digitizing the old process of checking out physical drawings. There's been no evolution of the process. Nobody (that I'm aware of), has looked at the way software is built, tried to extract lessons from that, and implement a subset of those in other walks of engineering. Managing models, assemblies and dependencies is easily one of if not the most annoying parts of my job, and could be improved drastically with a Git inspired tool.
I want Git for CAD so badly. There are many ways and reasons that Git and source control can't apply 1:1 with CAD, but I think someone should investigate. Git for CAD could allow me to change a hole in a model, while a co-worker changes the chamfers of that part, as well as the assembly where my part bolts to another, all at the same time. In the mechanical engineering world right now you either have files strewn about your literal or digital desk, or you have a digital filing cabinet (PDM) that you and your colleagues can check drawings out of (and hopefully check back in). The digital filing cabinets cost thousands if not tens of thousands per year per person, and there are few company's who make them.
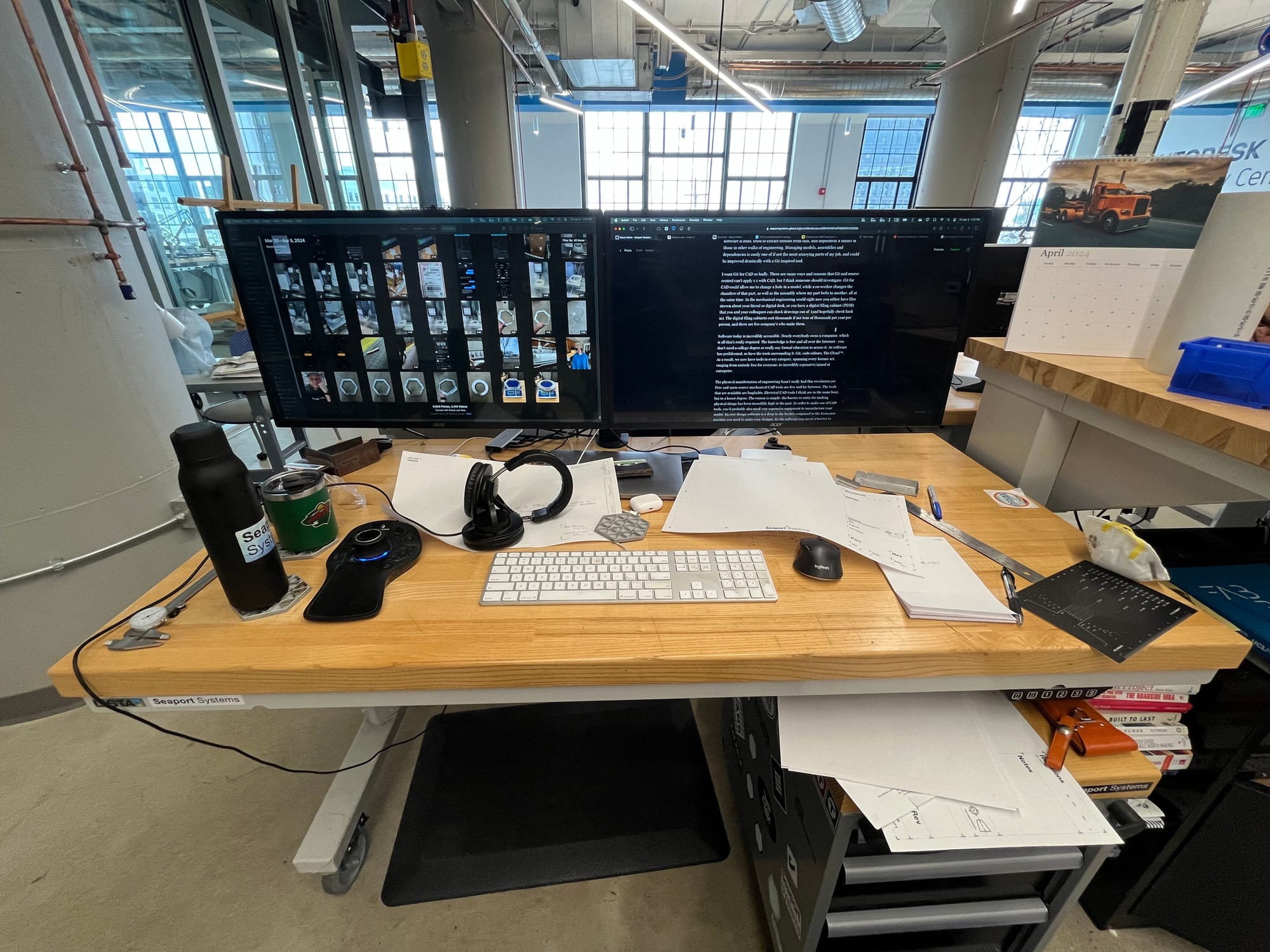
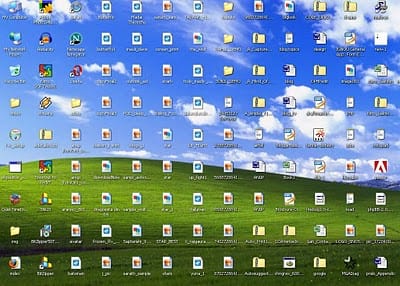
Neither of these are particularly effective strategies for organization...
Software today is incredibly accessible. Nearly everybody owns a computer, which is all that's really required. The knowledge is free and all over the Internet - you don't need a college degree or really any formal education to access it. As software has proliferated, so have the tools surrounding it. Git, code editors, The Cloud™. As a result, we now have tools in every category, spanning every feature set, ranging from entirely free for everyone, to incredibly expensive/aimed at enterprise.
The physical manifestation of engineering hasn't really had this revolution yet. Free and open-source mechanical CAD tools are few and far between. The tools that are available are laughable. Electrical CAD tools I think are in the same boat, but to a lessor degree. The reason is simple: the barrier to entry for making physical things has been incredibly high in the past. In order to make use of CAD tools, you'd probably also need very expensive equipment to manufacture your model. $2,000 design software is a drop in the bucket compared to the $100,000 machine you need to make your designs. So the software was never a barrier to entry, it was the equipment.
Now, 3D printers are a household appliance. You can go to a physical store and buy one right now. You can go on Amazon, give Jeff $169.99, and a disenfranchised minority will deliver it to your door, tomorrow. In less than 48 yours you can start fabricating just about anything you want. $169.99 is a very accessible price point for people, schools, small businesses. $2,000 not so much. Now the barrier to entry is not the equipment, it's the software.
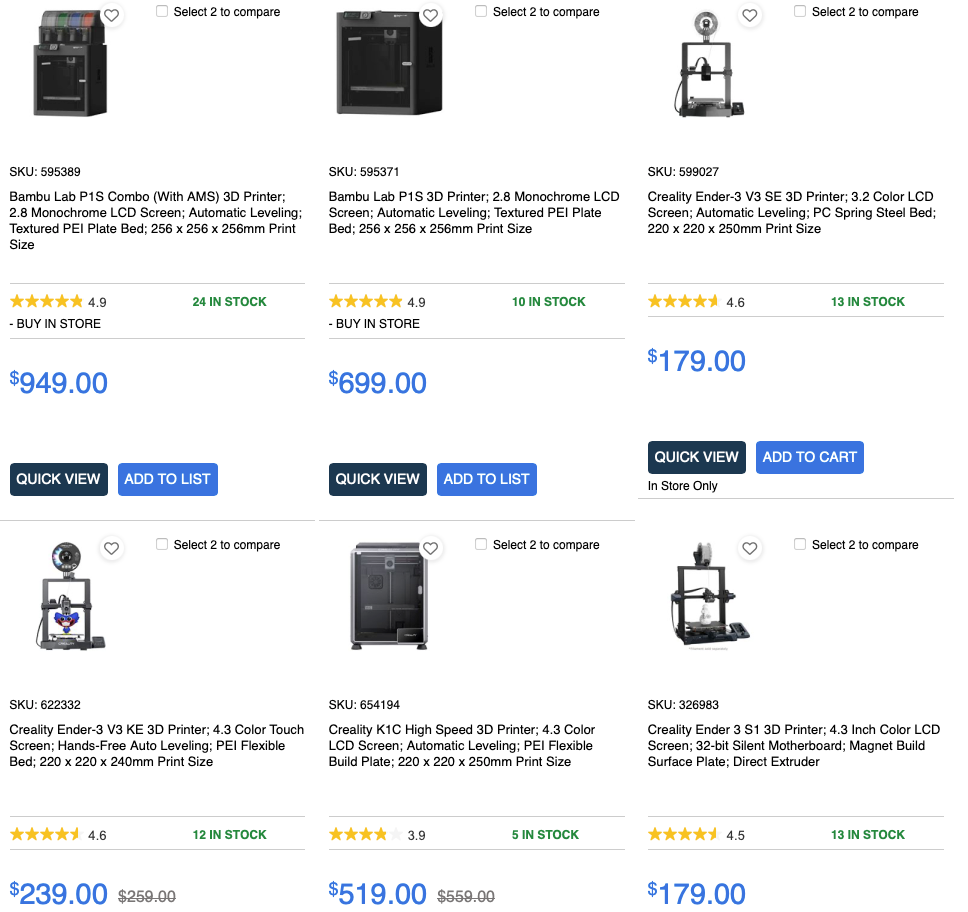
Note: $2,000 is very much an average guestimation. Fusion 360 is free for a couple of years for personal use, before becoming ~$650/year; while basic NX is at least $7,000 per year. Commercial solutions can be found anywhere in between, but the barrier is still drastically higher than tools for building software.
Writing is a fascinating comparison to this. I'm sure there was a time when pencils and paper were prohibitively expensive. There was also probably a time when typewriters were too expensive, and so people were stuck writing by hand while the well off could type. I started my schooling at a point where a school might have a computer lab with a class worth of computers to share amongst the whole school. When I finished high school, it was basically expected that every single student have their own personal computer.
Beyond collaboration tools, I think there are tons of frameworks and ways of thinking that have come out of the recently booming software sector that haven't spread to other industries. I'm hoping that the availability of affordable fabrication equipment (3D printers, laser cutters, plotters) kicks off a similar revolution in the tools needed to create the ideas to be fabricated.
This Week
Top Collar
Huge week for the top collar: the first part has been machined! Check it out!
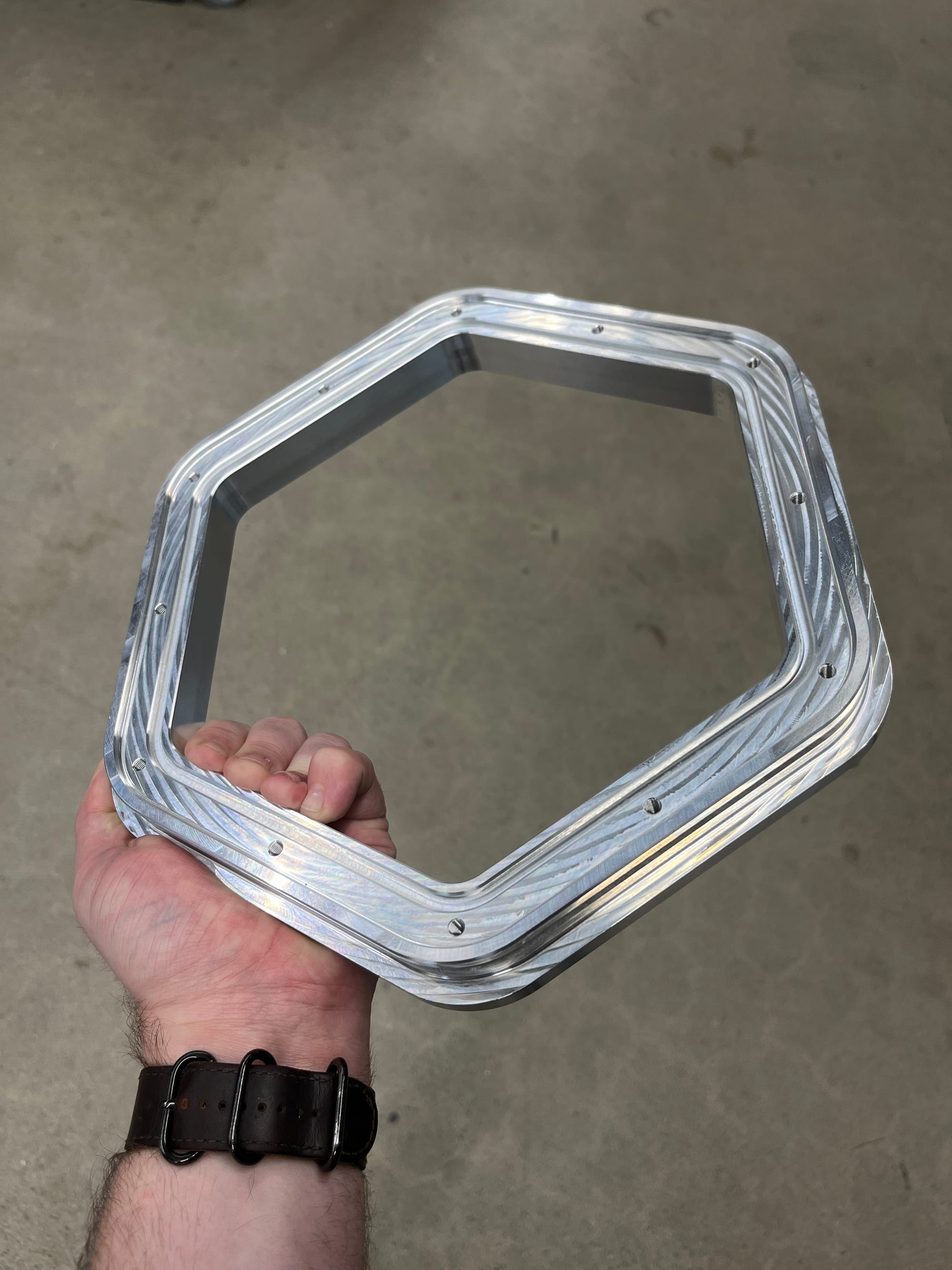
Once Zack pointed me in the direction of VersaGrips, the work holding problem was solved and machining was incredibly straightforward. It was almost boring how uneventful the two operations were. The most excitement was cutting the radial o-ring groove with the woodruff cutter, which still felt incredibly routine.
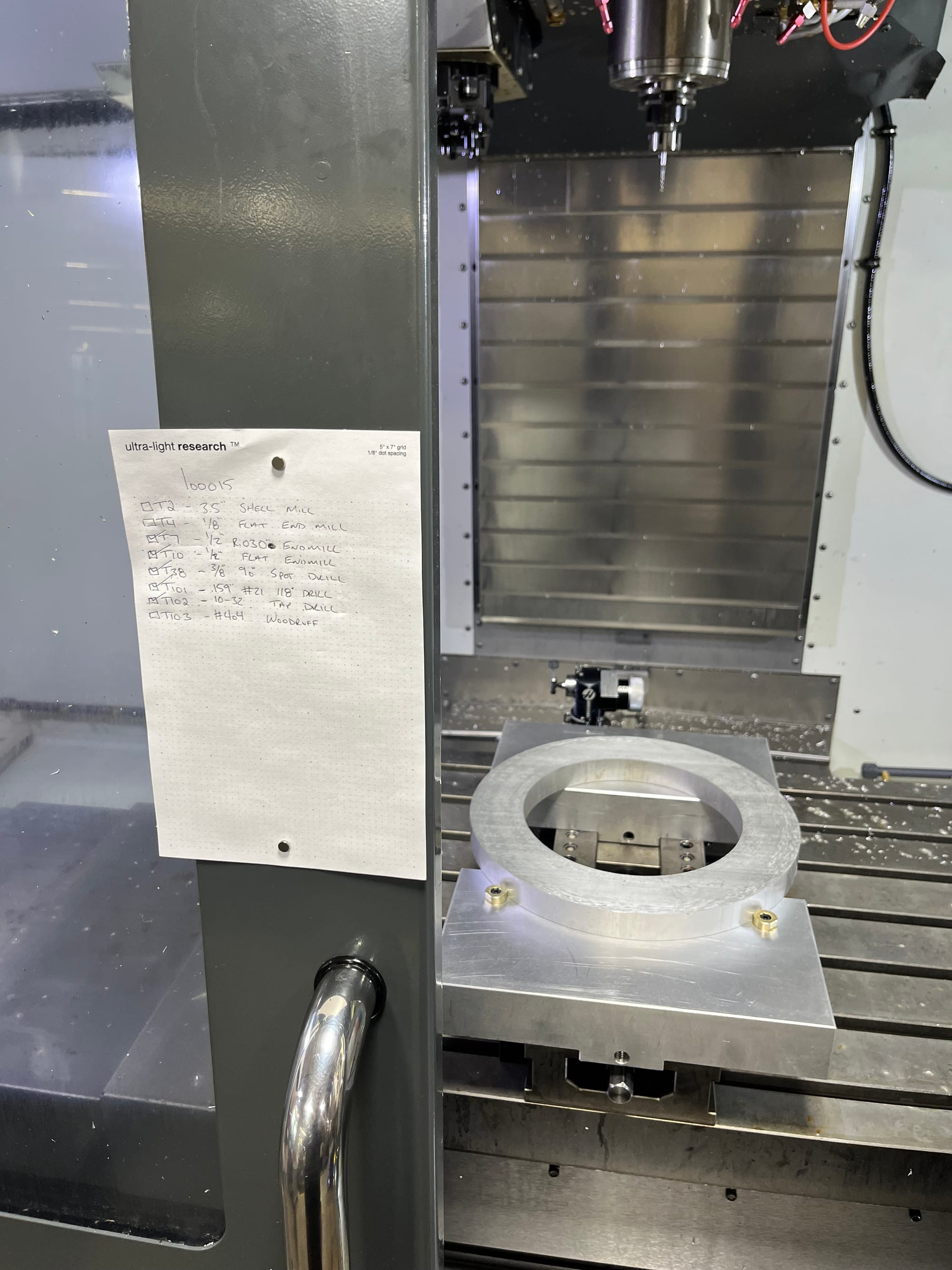
I'm really proud of this piece. It's one of the biggest machined parts I've ever fabricated, it's one of the more complex parts I've fabricated for sure. It doesn't really have anything on some of the insane aerospace parts people are making every day, but maybe one day I'll get there. Crazy complexity is mesmerizing, but I think it's so much cooler when a simple lever accomplishes the same thing as a 40 part, crazy critically dimensions assembly of parts.
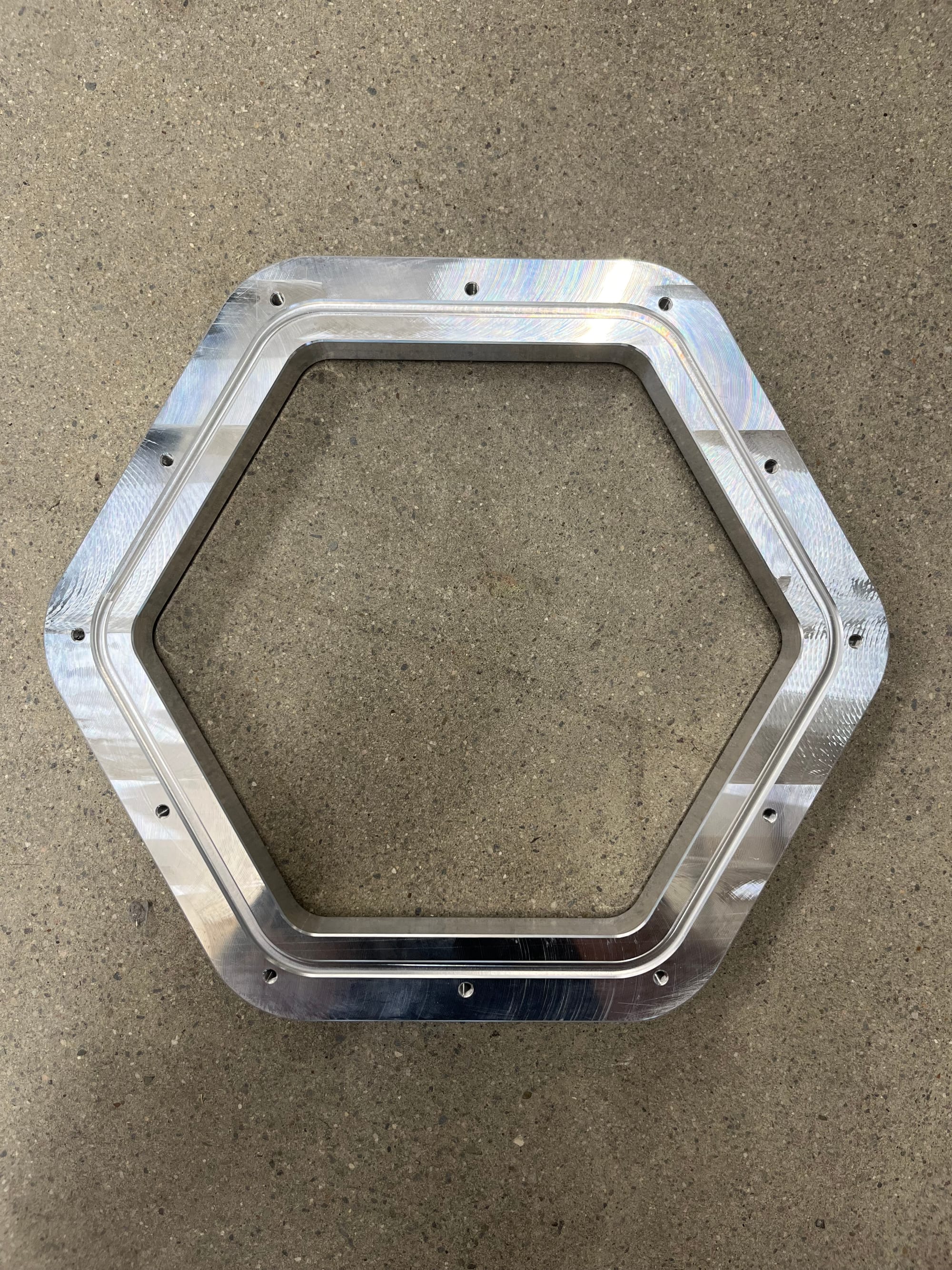
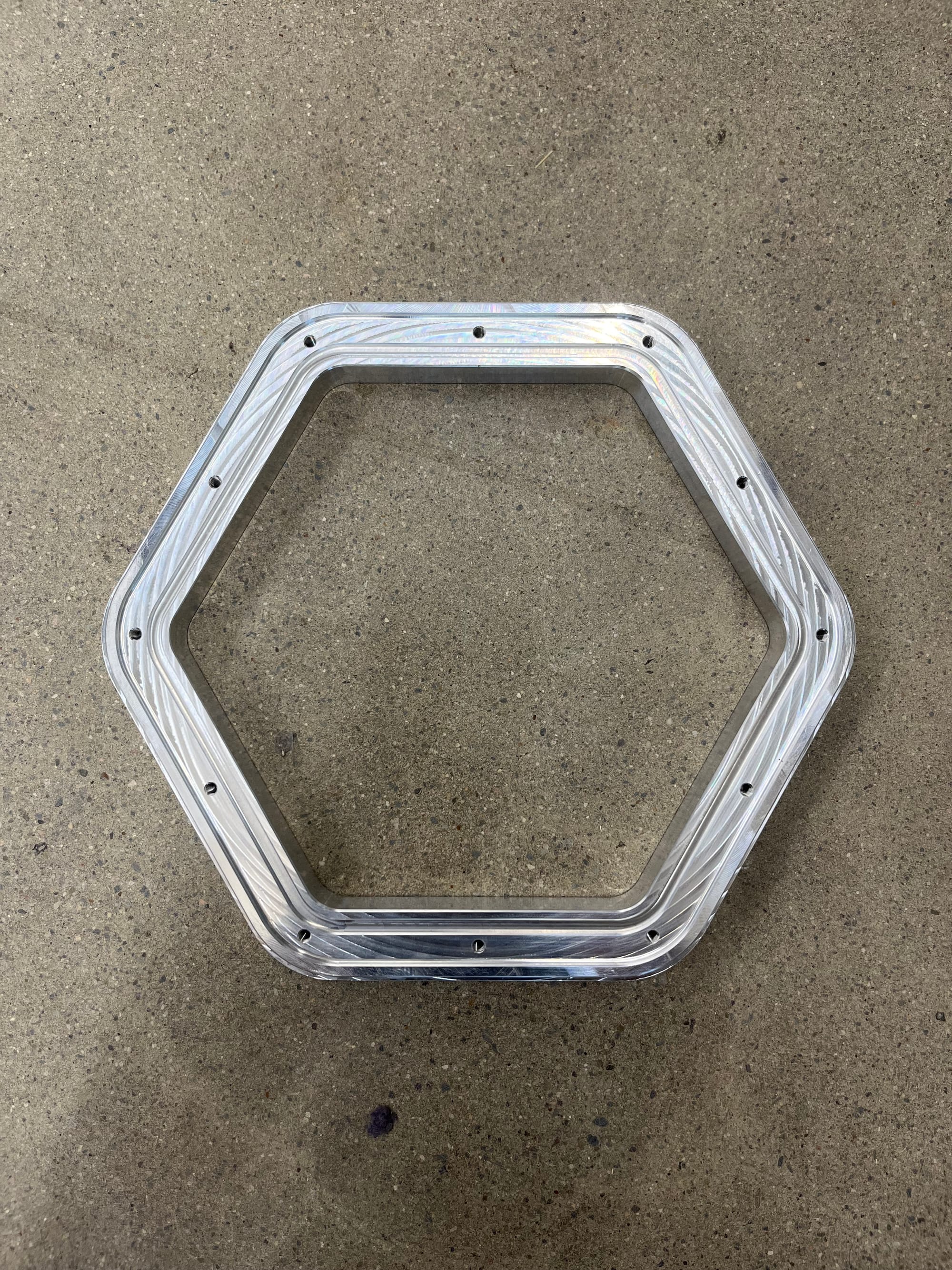
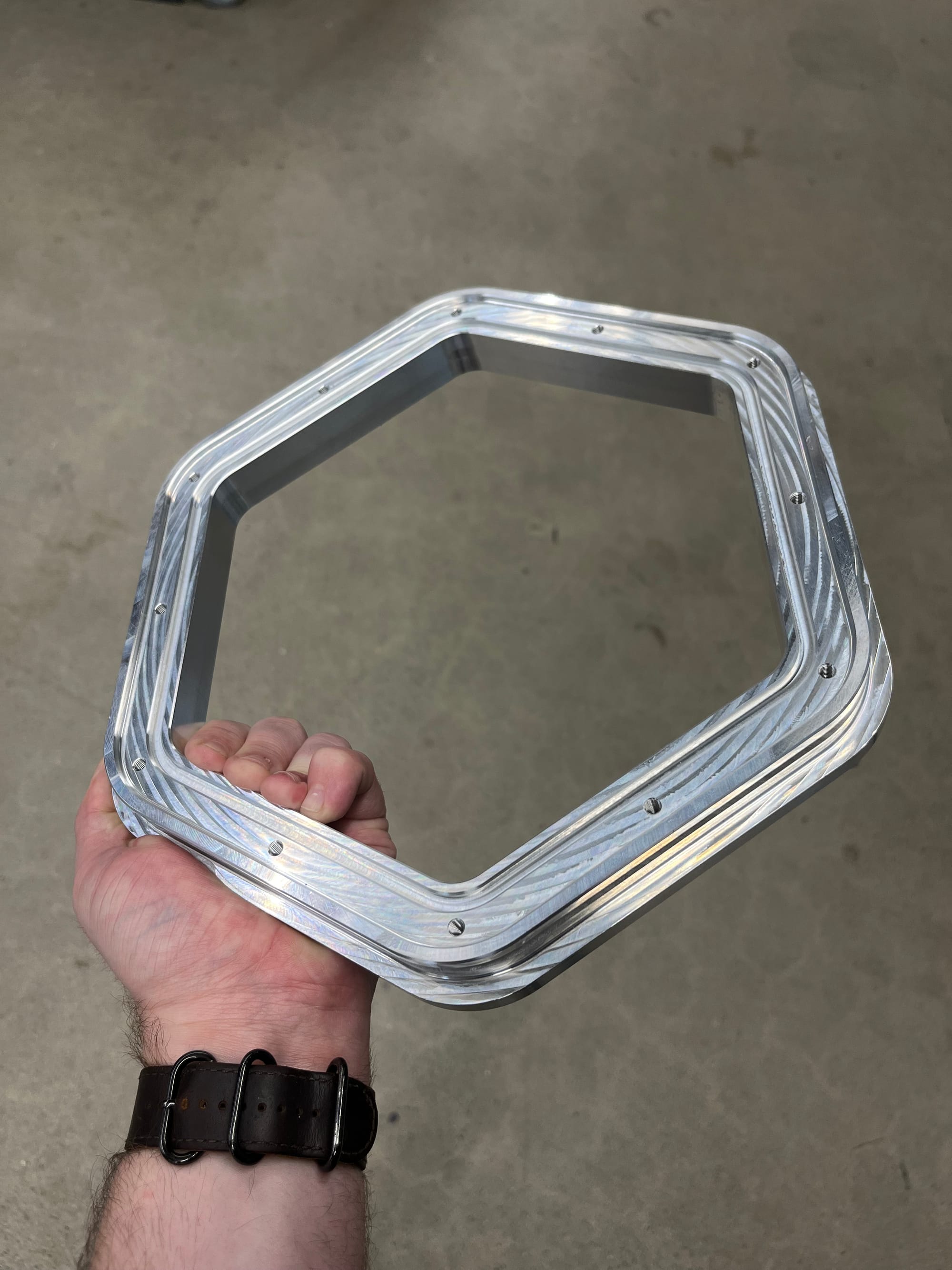
100015/01 Top, Bottom, Handheld
I built this piece around 12" OD, 8" ID tube stock I found on McMaster. The tube stock is great because it's: super cheap, about $30; not hard to source; and I need to remove very little material. If I sent this part away, I almost guarantee they would mill it from a 12"x12"x1.25" block of Aluminum. For reference, that's a $139 just for the metal; and it'd weigh 17.640 pounds. The tube stock is 6.315 pounds. My final part weighs 2.615 pounds. So I could either waste 85% of the original stock, or only 59%. I'm not a sustainability nut, but I do what I can. I try to pick recyclable materials, materials that aren't absolutely horrible for the environment, and I try not to make unnecessary waste. Not taking the easy way out, and saving waste on this part feels great

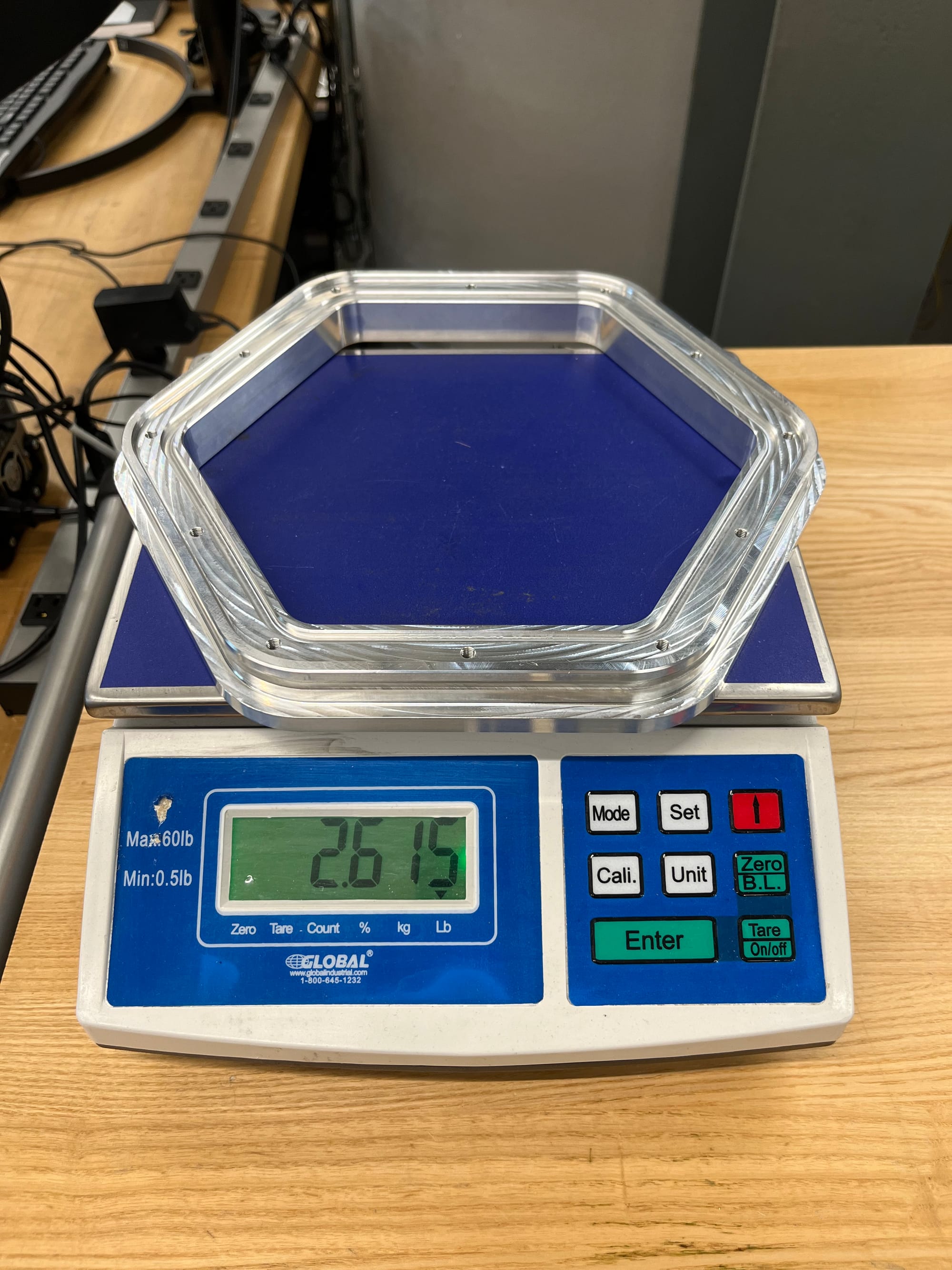
100015/01 Starting Weight (Left) and Final Weight (Right)
Paperwork
A lot of uninteresting back office work. E-mails, meetings, calendar invites, accounting, etc... Not very noteworthy stuff, but the fact that I actually did it is!
Antenna Testing
Antenna testing for the DB-X is in progress. No publishable or actionable results yet, but I'm actively working on it. Stay tuned for continued progress next week.
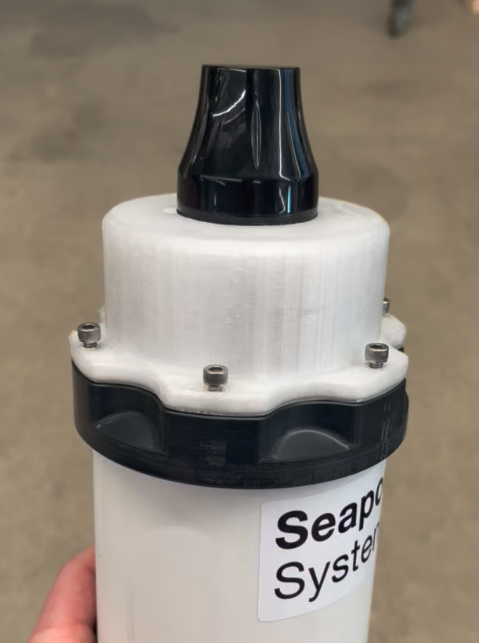
Next Week
Antenna Testing (Continued)
The DB-X right now has two GPS units, one standalone and another on the cellular modem. The big step for next week is to figure out how to consolidate. 2 potential paths forward are clear: get an antenna splitter that can share the GPS antenna between the two modems; pull data right from the cellular antenna.
I think the antenna splitter will probably be the way to go. The drifters use GPS to record location and current speed. I'm not exactly sure why the cellular modem needs GPS, maybe it doesn't, maybe it uses it for a warm start type functionality. The separate GPS almost certainly will provide higher quality data than a low cost, low functionality unit built into the cellular modem. We will see how the quality of the data varies though.
Wins
Cruise Ship Season Is Back
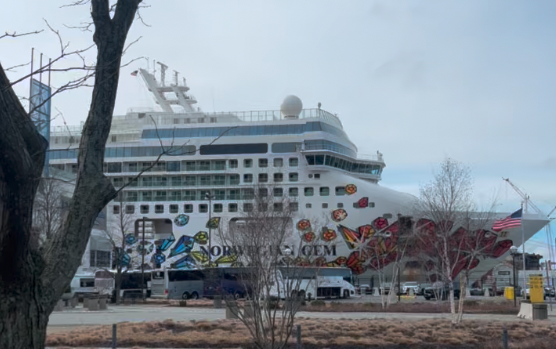
The back door of my office opens up to Boston's cruise ship terminal. Pretty much every day April to October there are cruise ships docked. Makes my walk down the pier more enjoyable!
Strawberries
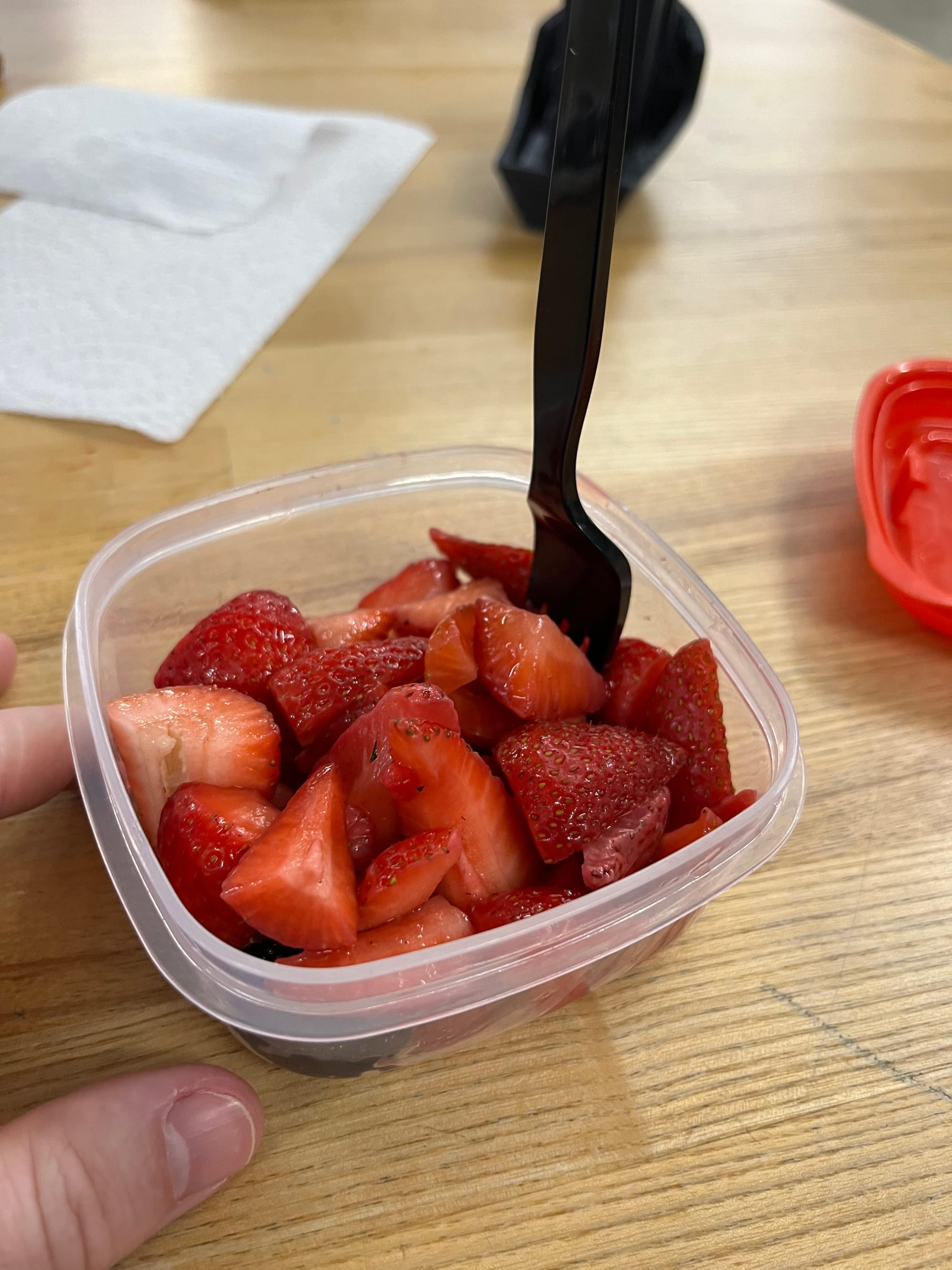
Losses
Exercise
Didn't really exercise as much as I'd hoped. Every night I felt like it took a backseat to something else...
This baguette I saw on the platform at South Station
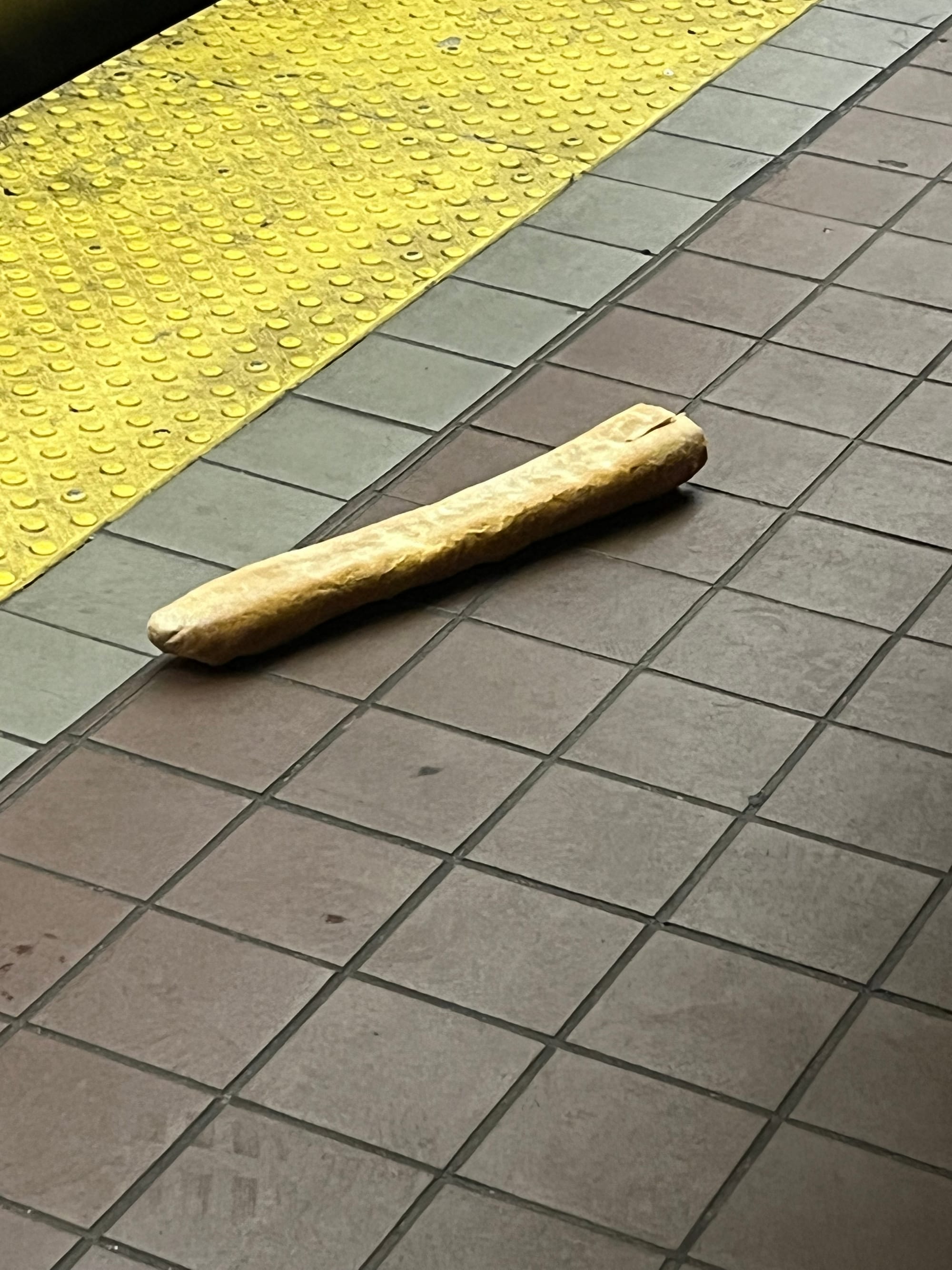
Train Track of the Day
Outro
Roll the credits. That's all I got for this week. Have a good weekend, or don't, that's up to you. Thanks as always if you've made it this far! Maybe pass it along to someone you think might find it interesting ¯\_(ツ)_/¯